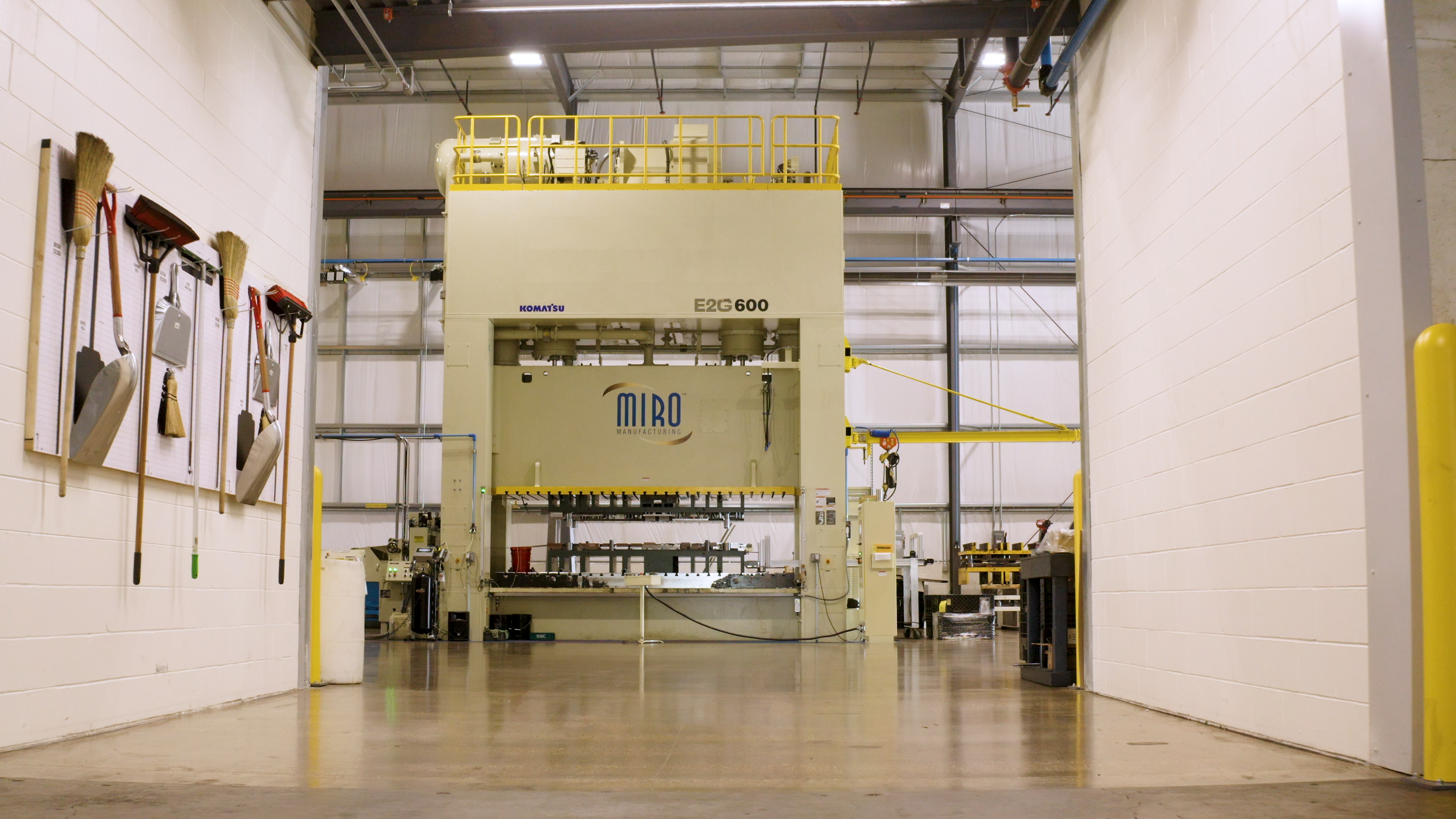
What do your car, your home washing machine, and your charcoal grill have in common? They all contain metal components formed by precision metal stamping.
These three everyday items contain varying amounts of metal components of different shapes and sizes – this speaks to the versatility and capabilities of metal stamping.
Essentially, metal stamping transforms sheet metal into custom-shaped parts. Sheet metal is strong and can be produced in various thicknesses to suit the application of the part. Precision metal stamping makes extremely tight tolerances possible, helping ensure stamped parts fit together, function properly, and are interchangeable.
As a highly automated metal fabrication process, metal stamping is efficient, and thanks to computer-aided design (CAD), designs can be repeatable for consistent high quality and precision.
Benefits of Precision Metal Stamping
In industries that require every component to meet exacting specifications and high quality standards, the benefits of precision metal stamping cannot be overstated.
-
High Accuracy and Consistency
Programmable presses are highly automated, reducing human error and achieving a high level of precision. This automation ensures consistent quality and repeatability across large production runs, which is essential for industries with strict quality requirements, such as automotive and aerospace.
-
Cost-effective
Before the integration of automation technology, metal stamping was labor-intensive and required expensive resources, making stamped parts expensive. Today’s technology and automated machines drastically reduce the amount of labor required, reducing production costs for high-volume runs. The added precision of CAD tooling design has the added benefit of reducing material waste.
-
High Production Speed
Press cycle time depends on several factors, including the type of press, type and thickness of material, characteristics of the piece part, and the die used. High-speed presses are capable of producing large volumes of identical parts. Compared to other manufacturing methods, the production time required for stamping is typically greatly reduced.
-
Flexibility and Versatility
Stamping requires the use of tools and dies to cut and shape the metal, meaning it’s possible to manufacture piece parts in a wide range of shapes and sizes. This flexibility makes stamping a suitable fabrication process for a variety of industries and applications.
-
Capable of Producing Complex Parts
The use of stamping dies makes it possible to create designs and shapes that would be too difficult, too costly, or impossible to manufacture with other methods.
-
Improved Strength
With stamping, you can incorporate features like reinforcing ribs or flanges to enhance the rigidity of the piece part.
-
Material Efficiency
Stamping typically uses less material than other methods, reducing material waste and cost.
What to Consider When Choosing a Manufacturing Partner
Selecting a manufacturing partner is not a decision that should be taken lightly. Any potential partner will be an integral part of your supply chain and should be vetted thoroughly to ensure they will help, not hinder your operations. As you investigate contract manufacturers, we recommend taking these three factors into account: capability, collaboration, and trust.
-
Capability
Do they have the capabilities to manufacture your project? Can you trust them to tell you if they don’t? Unfortunately, some manufacturers will say they can complete your project even if it’s outside their wheelhouse, just to get the job. Identifying potential partners who are upfront about what they can and cannot do is vital.
-
Collaboration
So you have found a potential manufacturing partner with the appropriate capabilities. Next, you need to evaluate their willingness to work with you to refine your project for optimal machinability. There is a significant difference between manufacturers who do the work as-is and those who will advise you and help you make your components better.
-
Trust
Finally, it’s important to find a partner you can trust. Can you rely on them not only to collaborate, but to openly communicate with you? Have you seen proof of the quality of their work, both office-side and production-side? Do their company values align with yours and what you are seeking in a partnership?
Putting potential contract manufacturers through this evaluation process will help you identify the best manufacturing partner for your needs.
Miro is an Ideal Manufacturing Partner for Precision Metal Stamping
Thanks to technological advances, metal stamping continues to be a key manufacturing method for producing superior piece parts. Its accuracy, repeatability, and versatility make it a necessary fabrication process for countless industries.
Miro started in 1988 as a tool and die shop, so we have decades of experience and stamping expertise. We understand the importance of collaboration to ensure the efficiency of design, cost, and production, which is why we take our role as a strategic partner in your supply chain seriously.
Our motto “from start to part” illustrates our steadfast commitment to you as your manufacturing partner to guide you throughout the journey from project inception to full production. You can trust us to be upfront about our capabilities and to deliver your project with the highest quality.
Let us quote your next stamping project and experience the Miro difference for yourself: https://miromfg.com/rfq/.