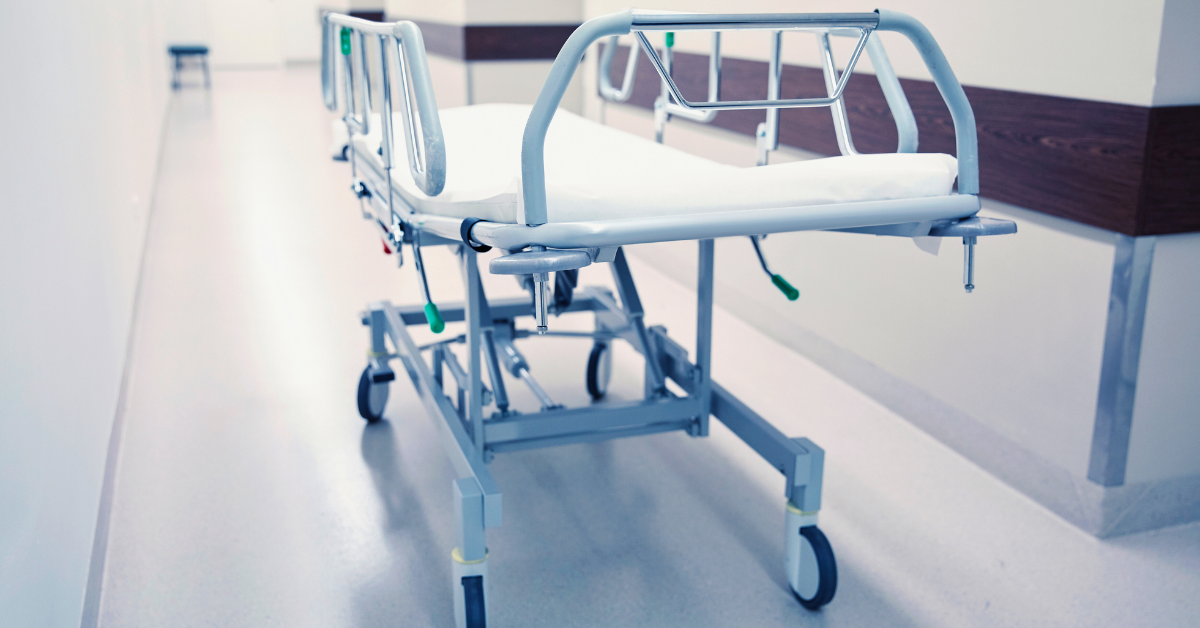
Miro Manufacturing serves a variety of industries: agriculture, appliance, heat transfer, heavy truck, medical, power distribution, and recycling. Though one might think these industries have little in common, we have uncovered through our decades of experience that they share one critical thing: complex challenges.
While other contract manufacturers shy away from such challenges, Miro takes them in stride. We have a proven track record of successfully managing projects that involve developing new parts, creating tooling, and optimizing existing parts and tooling simultaneously for improved performance.
In this blog, we’ll explore how Miro delivers quality sheet metal components for medical equipment manufacturers.
How Miro Manufacturing Creates Premium Components for Medical Device Manufacturers
The term “medical equipment” encompasses everything from simple tools like tongue depressors to devices that diagnose, monitor, and/or treat medical conditions, to implantable devices, and countless other items required by doctors and medical facilities to care for patients.
At Miro, our extensive knowledge and experience in sheet metal manufacturing lends itself to the manufacture of non-implant, durable medical equipment, such as components for patient transport, and for use in the field and medical facilities.
Regulatory Compliance
- Medical device manufacturers look for contract manufacturers that adhere to strict standards set by the International Standards Organization (ISO).
- Miro underwent the lengthy process required to achieve ISO 9001:2015 certification; we are audited internally and externally every year. (In fact, our certification was renewed in January 2024 after undergoing a comprehensive recertification audit). Adherence to standards and continual improvement are in our blood.
- Our customers can trust that Miro-manufactured components will meet the highest quality and safety standards required by the medical industry.
Quality Control
- Our customers expect rigorous quality assurance, which is why high quality is our mandatory standard.
- At Miro, quality control isn’t just a department, it’s our standard operating procedure. We consider quality the responsibility of everyone who touches a part, and we review parts throughout the entire manufacturing process–not just at the end–to ensure our customers receive only the highest quality. Rest assured that components don’t leave our shop until they’re right.
Technical Expertise
- Miro is known for its specialized knowledge and advanced technology.
- Though Miro started as a tool and die shop, we have invested in our people and our equipment so we can always produce the best parts. Many of our employees have worked in metal manufacturing for decades; in that time, they’ve adopted and perfected new technologies that make projects more efficient, accurate, and cost-effective for our customers.
- By expanding our capabilities and adding advanced technologies, we can be a one-stop show to better serve our customers.
Capabilities
- Metal stamping
- Fabrication, including
- Laser cutting
- Waterjet cutting
- Press brake forming
- Welding
- Tooling design
- Precision CNC machining, including
- Wire EDM
- Turret punch press
- Assembly and kitting
Supply Chain Management
Our extensive capabilities allow us to keep most manufacturing processes in-house, which simplifies the supply chain for our medical manufacturing clients.
Engineering Support
One thing our customers appreciate about us is our ability to recommend project modifications that improve manufacturability. We provide guidance and offer suggestions to improve manufacturability and reduce production time and costs.
Specialized Equipment
Medical equipment manufacturing requires precision fabrication. Stamping, laser cutting, and press brake forming are capabilities we often utilize to serve this industry, which is why we regularly invest in the best equipment–in recent months we have added a 330-ton press brake and a second fiber laser.
How Miro Serves the Medical Equipment Manufacturing Industry
Given the role durable medical equipment plays in saving lives and improving patient care, Miro is proud to support this industry with our sheet metal stamping, fabrication, and machining capabilities. What we manufacture often falls under either the durable medical goods or patient transport category. One thing Miro does not manufacture is medical implants.
We have worked with our customers “from start to part,” collaborating with engineers throughout the design phase, educating them on sheet metal forming characteristics to optimize designs for manufacturing. Miro also designs and builds special tooling to manufacture the end parts.
Why Miro Manufacturing is Your Ideal Partner for Medical Manufacturing Projects
Miro’s suite of sheet metal manufacturing capabilities, including stamping, fabrication, and CNC machining, make us a key partner to medical equipment manufacturers, especially those looking to re-shore their manufacturing or narrow their list of domestic suppliers.
Our customers expect quality parts, and we deliver. To us, “quality” is more than just a word on our website or the name of a department: it’s our mandatory standard that we are committed to continually improving to exceed expectations.
Because we have capabilities that enable us to complete so many processes in-house, we can accurately forecast and hit delivery dates to keep our customers’ projects on schedule.
Our approach to contract manufacturing is to build collaborative relationships. As your manufacturing partner, we are here to guide you through your project from inception to production. We are proud to offer competitive pricing for the outstanding service we provide.
Let us quote your next durable medical equipment project: https://www.miromfg.com/rfq/.