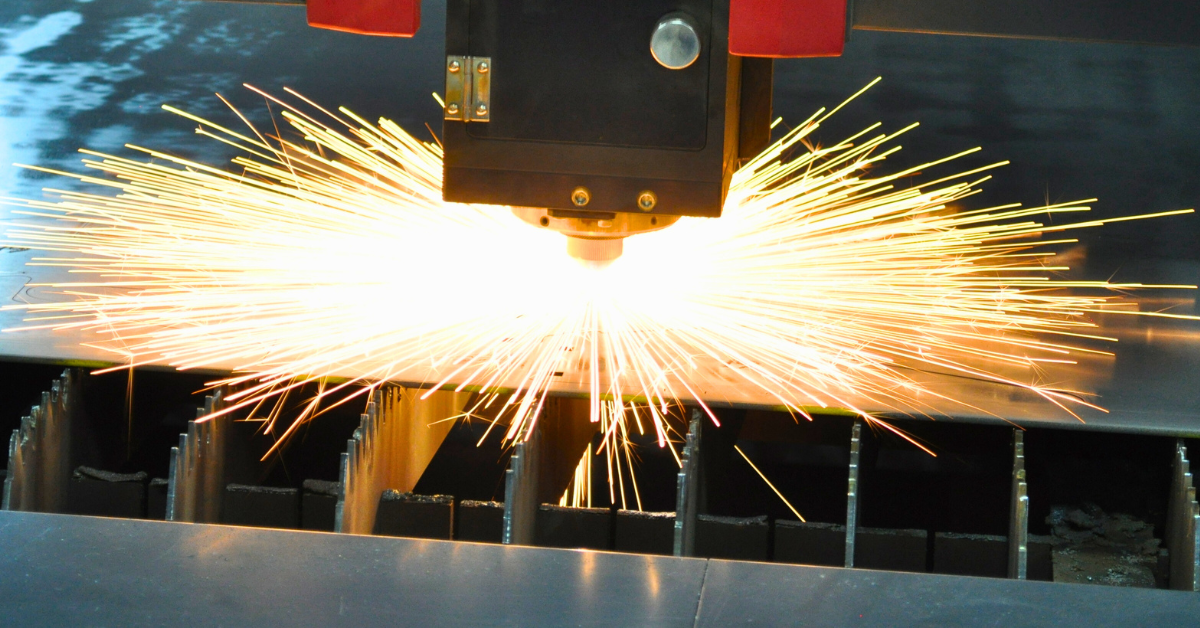
For precision sheet metal fabrication, Miro Manufacturing sets the industry standard. From high-precision cutting techniques to advanced bending and forming processes, Miro’s capabilities ensure that every component meets exacting specifications. Our state-of-the-art equipment and commitment to quality make us the ideal partner for complex, high-volume projects across industries such as power distribution, durable, non-implant medical goods, and appliances.
Advanced Cutting Techniques
Laser Cutting: High-Speed Precision
Laser cutting is one of the most efficient methods for cutting sheet metal, offering unparalleled accuracy and minimal material waste. Miro’s 8000-watt fiber lasers are game-changers for customers needing high-speed, cost-efficient production. These advanced machines are fully automated, maximizing throughput while ensuring each cut is precise, clean, and consistent. Our 4500-watt CO2 laser complements this capability.
Miro Manufacturing’s investment in cutting-edge fiber laser cutting technology enhances our precision, efficiency, and cost-effectiveness. Our Mitsubishi systems deliver industry-leading capabilities and processing efficiency.
Key Benefits of Miro’s Laser Cutting Services
- Unmatched Precision – High-speed laser cutting ensures accurate, clean cuts with minimal waste.
- Exceptional Efficiency – Automated load/unload systems allow continuous operation, reducing lead times.
- Versatility Across Materials – Cuts carbon steel up to 1” thick, stainless steel up to ¾” thick, and aluminum up to ½” thick.
- Cost Savings – Optimized resource utilization reduces operational costs while maintaining high-quality output.
- Automation for Increased Productivity – Advanced material handling capabilities support high-volume production with minimal manual intervention.
- Quality Assurance – Smart monitoring systems enhance process stability and ensure consistent cut quality.
Our fiber laser technology, combined with a 4500-watt CO2 laser, enables us to handle a broad range of materials and projects, from intricate custom components to large-scale production runs. Miro’s laser cutting services provide superior edge quality, often eliminating the need for secondary finishing operations and improving overall cost-efficiency.
Waterjet Cutting: Cold Processing for Versatility
For applications where heat distortion must be avoided, waterjet cutting is the ideal solution. Miro’s high-pressure waterjet system provides precision cutting across various materials, ensuring superior results without thermal damage.
Benefits of Miro’s Waterjet Cutting Services
- Superior Edge Quality – Produces smooth, precise cuts, reducing or eliminating secondary finishing requirements.
- Extreme Accuracy – Achieves tight tolerances, ideal for applications requiring exacting standards.
- Versatility Across Materials – Effective for metals (steel, aluminum, titanium), stone (granite, marble), composites, plastics, rubber, glass, and more.
- Preservation of Material Properties – Cold cutting prevents hardening, warping, or material stress.
- Eco-Friendly Process – Produces no hazardous fumes or liquid waste, with recyclable abrasive materials reducing environmental impact.
Miro’s Waterjet Cutting Capabilities
- High-pressure system cuts materials up to 7” thick.
- Maximum stock sheet size of 72” x 144” allows for large-format part processing.
- Advanced nesting software maximizes material usage, minimizing waste and cost.
- Precision taper control system ensures consistent accuracy without sacrificing productivity.
With decades of experience and state-of-the-art equipment, Miro’s waterjet cutting services are designed to provide cost-effective, high-quality manufacturing solutions. Whether you need intricate shapes or large, complex components, Miro delivers unparalleled precision and reliability.
CNC Turret Press Services: Flexible, Cost-Effective Part Production
Miro Manufacturing’s CNC turret punch press bridges the gap between dedicated stamping dies and laser cutting operations, making it an ideal choice for low- to mid-volume part runs that incorporate stamped features.
Benefits of CNC Turret Press Punching:
- Upfront Cost Savings on Tooling – Eliminates the need for dedicated stamping dies, reducing initial investment.
- Efficient Production for Low- to Mid-Volume Runs – Ideal for new product lines and incremental production scaling.
- Quick Setup and Turnaround – Allows for rapid prototyping and small-scale production.
- High Precision and Consistency – Ensures uniform quality across all punched parts.
Miro’s CNC Turret Press Capabilities:
- Punching Capacity – 22.5 tons, accommodating a broad range of part dimensions.
- Sheet Size – Handles sheets up to 49.2” x 49.2”.
- Material Thickness – Processes materials up to 0.25” thick, including:
- Aluminum
- Carbon Steel
- Copper
- Stainless Steel
This versatile approach allows businesses to launch new product lines with ease, starting with low-volume production and scaling up seamlessly to dedicated stamping tooling as demand grows. By leveraging our turret press, customers benefit from a cost-effective, flexible, and highly efficient manufacturing process.
CNC Machining: Precision and Repeatability
For our clients that require complex components with intricate geometries and tight tolerances, CNC machining is often our go-to process. Miro Manufacturing’s CNC machining capabilities are tailored to meet the diverse needs of our clients, particularly in medium production volumes. We prioritize close collaboration from initial product development to completion, ensuring seamless transitions from prototype to production while mitigating potential manufacturing issues.
Benefits of CNC Machining
- Unmatched Precision and Accuracy – CNC machining ensures exact replication of complex geometries with minimal variance, making it ideal for industries requiring high tolerances.
- Reduced Waste – Precise material removal optimizes resource usage, minimizing scrap and reducing costs.
- Design Flexibility – Rapid reprogramming allows for quick design changes, prototyping, and custom production.
- Cost-Effectiveness – Automated machining reduces labor costs while ensuring consistent quality.
- Scalability – Whether producing small batches or large-scale orders, CNC machining provides seamless scalability without compromising precision.
Miro’s CNC Machining Capabilities
Miro Manufacturing is equipped to machine various materials, accommodating a maximum workpiece weight of 3,000 lb.
- Materials We Machine:
- Carbon steel
- Tool steel
- Hardened tool steel
- Stainless steel
- Aluminum
- Plastics
- Machine Travel Dimensions up to 86” x 34” x 30” – Allowing for fewer adjustments, increased accuracy, and greater efficiency, especially for larger components.
- Precision Turning: Capable of machining cylindrical or rounded parts with diameters ranging from 20” to 40”, ensuring accuracy in rotational applications.
- Surface Grinding: Miro provides precise surface grinding for parts up to 20” x 40”, ensuring a high-quality surface finish with dimensional accuracy for enhanced part performance.
Bending and Forming: High-Capacity Press Brake Systems
Press Brake Systems: Versatile and Precise Forming
Miro Manufacturing’s CNC press brake systems offer precision forming capabilities that ensure exceptional consistency and accuracy across projects. Our press brakes provide significant advantages, including:
- Increased versatility for various applications
- Enhanced capabilities to handle complex geometries
- Greater precision and consistency in formed parts
- Improved efficiency and productivity with CNC automation
- Better quality control through real-time monitoring
- Faster production through high-speed bending processes
Miro’s Press Brake Capabilities
Our forming capabilities include some of the most advanced press brake systems in the industry.
- Large Part Forming: Our largest brakes can form parts up to 14’ in length, making them ideal for large-scale applications.
- Material Versatility: Miro Manufacturing can form materials up to 0.5” thick, accommodating:
- Aluminum
- Brass
- Carbon steel
- Cold-rolled steel
- Copper
- Galvanized steel
- Hot-rolled steel
- High-strength steel
- Stainless steel
- Diverse Press Brake Work Centers: With multiple CNC press brakes, Miro provides:
- Tonnage capacities from 60 to 360 tons
- Bed lengths from 8′ to 14′, supporting various part sizes and complexities
- Industry-Leading Technology: Our SafanDarley H-Brake Ultra 360-ton, 14-foot CNC press features cutting-edge automation and precision.
- The E-Bend L Blue system uses dual blue lasers to continuously monitor and adjust bending angles in real time, ensuring unmatched accuracy.
- Powered Lift Tables: These advanced tables streamline the handling and forming of large sheet metal parts, improving efficiency, reducing production time, and lowering overall costs.
- Seamless Process Integration: Our press brake forming services integrate seamlessly with our full suite of fabrication capabilities. By combining press brake forming with welding and CNC turret punch press services, Miro ensures that each component meets exact specifications before advancing to the next stage of production.
- This minimizes handling and lead times, optimizing the entire manufacturing workflow.
- Customers benefit from working with one provider for multiple fabrication processes, ensuring consistent quality, faster turnaround, and reduced project management complexity.
Automation and Robotics: Maximizing Productivity
Miro embraces automation to enhance manufacturing efficiency and ensure consistent quality. Our robotic welding systems produce high-precision welds while maintaining repeatability, speed, and compliance with stringent industry standards. This investment in automation allows us to meet high-volume production demands while reducing labor costs and minimizing production variability.
Why Miro? Your Trusted Partner in Sheet Metal Fabrication
Choosing Miro Manufacturing means partnering with an industry leader committed to quality, efficiency, and customer satisfaction. Our decades of experience, cutting-edge technology, and hands-on customer collaboration ensure that your project is executed seamlessly from start to part. With a fully integrated suite of fabrication services, we minimize lead times, streamline supply chains, and guarantee precision in every component we manufacture.
Let’s take your project from concept to completion with unmatched expertise in sheet metal fabrication. Contact Miro Manufacturing today to request a quote.