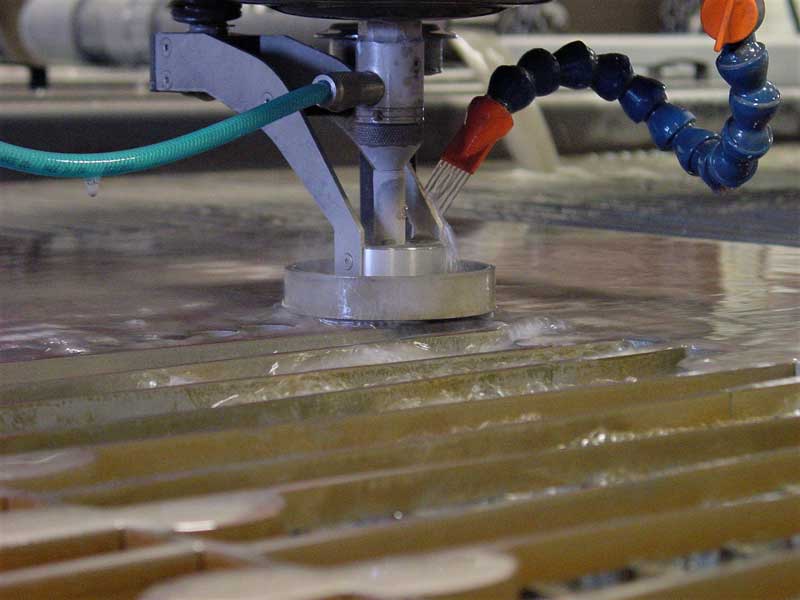
Precision and versatility are paramount to modern manufacturing. One cutting-edge technology that embodies these qualities is waterjet cutting.
At Miro Manufacturing, we leverage this advanced technique to deliver superior results for a variety of projects. In this blog, we delve into the process of waterjet cutting and its benefits so you can learn why it’s a crucial tool in modern manufacturing processes.
Understanding the Waterjet Cutting Process
The name “waterjet cutting” clearly explains the process: a high-pressure stream of water, often combined with an abrasive substance (we use garnet), is used to cut through materials. By directing a jet of water through a small, precisely engineered nozzle at great speed, the water achieves a force strong enough to cut through a wide range of materials.
When cutting through softer materials like rubber, foam, and some plastics, a jet of pure water will do. However, for harder materials like metal, the water must be mixed with an abrasive substance, for the cutting power to slice through tough materials.
The cutting process is meticulously controlled by CNC (Computer Numerical Control) systems, which ensure high precision and the ability to produce intricate shapes, sharp corners, bevels, and holes. The high level of control in waterjet cutting makes it an ideal process for industries where accuracy is crucial, such as aerospace, automotive, industrial equipment, and even food processing.
The Benefits of Waterjet Cutting
Superior Edge Quality
Waterjet cutting produces smooth, precise cuts. The superior edge quality of machined parts often eliminates the need for secondary finishing operations like deburring, streamlining the manufacturing process, saving you time and money.
High Accuracy and Tight Tolerances
Waterjet cutting offers exceptional accuracy and can achieve tight tolerances. For applications where even a slight deviation in tolerance can cause problems, waterjet cutting’s precision is critical. Whether you’re creating complex shapes or fine details, waterjet cutting can meet the exacting standards required in advanced manufacturing.
No Thickness Limitations
Unlike some cutting methods, waterjet cutting has no significant limitations on material thickness–it can handle anything from thin sheets to several inches thick materials. However, it’s worth noting that for very thick materials, holes may become narrower towards the bottom due to the nature of the cutting process.
Versatility to Cut Any Material
Unlike other cutting methods, waterjet cutting has the ability to cut virtually any material with precision, making it a valuable process for a broad range of industries.
Waterjet cutting can be used on these materials and more:
- Metals: Steel, aluminum, titanium, and more
- Stone: Granite, marble, and other natural stones
- Composites: Various engineered materials, such as Metal Matrix Composites (MMCs) and Thermoplastic Composites
- Plastics: From acrylics to polycarbonates
- Rubber and Foam: Ideal for gaskets and cushioning
- Glass: Including both regular and tempered glass
Preservation of Material Properties
When evaluating manufacturing processes for a project, you must consider the material’s properties. Waterjet cutting is a cold processing technique. Because it doesn’t generate property-altering heat, there’s no risk of hardening, warping, or other thermal effects that can occur with hot processing techniques like laser or plasma cutting. This makes it ideal for heat-sensitive materials and materials requiring precise mechanical properties.
Cost-Effective
Waterjet cutting is also a cost-effective solution for many projects. It boasts low operating costs and fast setup times, making it suitable for both short runs and large-scale production. The absence of secondary finishing operations further enhances its cost efficiency.
Environmentally Friendly
When considering the environmental impact of manufacturing processes, waterjet cutting stands out as a relatively environmentally friendly option. It produces no hazardous fumes, vapors, or liquid waste, and the used abrasive can often be recycled. Abrasive recycling prevents spent abrasives from ending up in landfills and saves manufacturers the disposal costs and environmental impact of transportation to the landfill. Additionally, the lack of a heat-affected zone means there is no material hardening or warping, reducing waste from flawed parts.
Efficiency Gains
Industry-leading waterjet machine manufacturers are continually developing ways to improve efficiencies and efficacy to better meet fabricators’ needs. They’re doing this by incorporating CAD/CAM interfaces to reduce manual labor and allow shops to spend more time cutting. They also forecast a shift to digital connectivity and Industry 4.0; Internet-connected machines will be more agile and able to function on a preventative maintenance schedule rather than the break-fix model.
The Miro Advantage
At Miro Manufacturing, our commitment to excellence is at the heart of everything we do. With decades of experience and a relentless dedication to quality, we pride ourselves on providing superior customer service that exceeds expectations.
We’re continually improving our large facilities with new machines to expand our capacity for high-volume projects. We understand the importance of precision for your parts, which is why we ensure every order is completed to the highest standards. On-time delivery is important to you, so it’s important to us. We’re dedicated to helping you stay on schedule and achieve your goals.
When you choose Miro Manufacturing, you’re gaining a trusted partner. Let us quote your next waterjet cutting project: https://miromfg.com/rfq/.