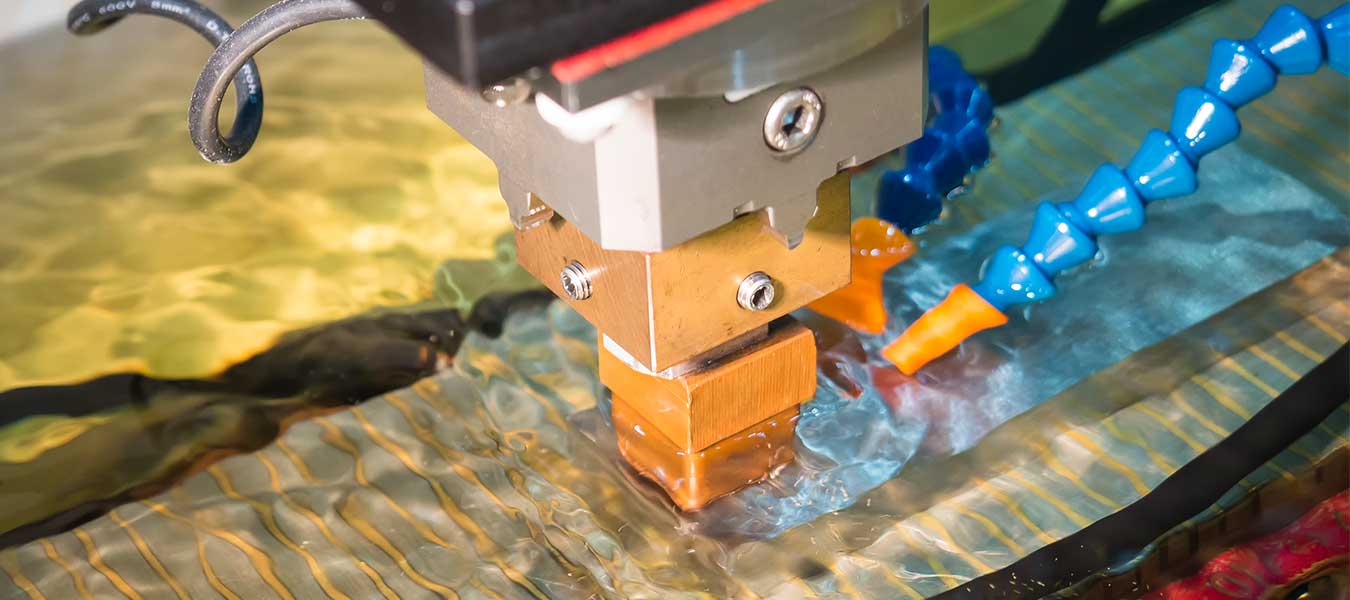
Electrical discharge machining (EDM), is a precision metal cutting process that uses electrical discharges to remove material from a workpiece. This manufacturing process is non-contact, incredibly precise, and capable of cutting various materials. Because EDM is a submerged process, it does not create high temperatures that could change the properties of the machined material and therefore has a minimal heat-affected zone.
EDM’s benefits, especially its high level of precision, make it well-suited for mold and die manufacturing, electronics manufacturing, the production of prototypes or small batches, and the aerospace and automotive industries.
Read on to learn about the pros, cons, and applications for 3 types of EDM machining – wire, sinker, and hole drilling – and how Miro can serve as your wire EDM manufacturing partner.
Wire EDM Machining
In wire EDM machining, an electrically charged hair-thin wire cuts electrical conductive materials, like brass and tool steels, through thermal erosion. Instead of a blade, the workpiece is cut by electrical sparks generated between it and the wire.
The cutting process takes place in deionized water, a dielectric fluid. This serves several purposes: it flushes away the tiny particles removed from the workpiece during machining, cools the process to reduce the heat-affected zone, and controls the sparking.
Here’s a high-level overview of the benefits and drawbacks of wire EDM.
Pros |
Cons |
High precision and accuracy for 2D profile cutting | Limited to 2D cutting and profile shapes |
Excellent for creating intricate patterns and fine details | Cannot create blind cavities or 3D contours |
Produces smoother surface finish compared to sinker EDM | Must start cutting from the edge of the workpiece or a pre-drilled hole |
More efficient for cutting thin materials | Less suitable for very thick materials |
Wire EDM utilizes an electrically charged wire for cutting, so no custom electrode is required | |
Faster setup time and generally quicker for large production |
Materials
Wire EDM is for conductive materials, including aluminum, carbide, copper and its alloys, Hastelloy®, hardened tool steel, Inconel®, Kovar®, stainless steel, and titanium.
Industry Applications
The features and benefits of wire EDM are well-aligned with the needs of high-precision industries like those below.
-
Aerospace
- Cutting turbine blades and vanes
- Fabricating engine components
- Producing landing gear parts
-
Automotive
- Engine cylinders
- Gears and gearboxes
-
Medical Devices
- Prosthetics
- Surgical instruments
- Surgical implants
-
Electronics
- Micro components, such as sensors and microchips
-
Tool and Die
- Molds and dies
- Stamping tools
- Extrusion dies
-
Jewelry/Watchmaking
- Intricate designs in precious metals
- Fine watch components
-
Research and Development
- Facilitating rapid prototyping of complex parts
- Enabling the production of experimental components
Sinker EDM
Sinker EDM shares many similarities with wire EDM. The primary difference is that in sinker EDM a workpiece is cut with a copper or graphite electrode, not a wire. The electrode also uses spark erosion to “cut” the workpiece; however, because the electrode has to be the shape of the feature you wish to cut in the workpiece, it’s better suited for machining blind holes or cavities too complex for traditional machining methods.
See the table below for an overview of the benefits and drawbacks of sinker EDM.
Pros |
Cons |
Capable of creating complex 3D geometries and blind cavities | Requires custom-made electrodes for each project, increasing cost and setup time |
Ideal for molds, dies, and deep cavities | Generally produces a rougher surface finish than wire EDM |
Can machine from anywhere on the workpiece without a starting hole | Slower machining process, especially for simple cuts |
Can produce irregularly shaped holes and features | Higher cost for less complex shapes that could be machined using other methods |
Materials
Sinker EDM is better suited for thicker, harder conductive metals, including aluminum, copper, nickel alloys, titanium, and tungsten carbide. It can also be used to machine conductive ceramics.
Industry Applications
Industries that require components with tight tolerances and minimal material stress can benefit from sinker EDM.
-
Mold and Die Making
- Molds for injection molding
- Dies for metal forming
-
Automotive
- Producing intricate parts for transmissions and powertrains
-
Aerospace
- Creating turbine blade components
-
Medical Devices
- Dental devices and implants
-
Electronics
- Producing molds for electronic casings
-
Jewelry/Watchmaking
- Fine watch components
-
Tool Manufacturing
- Producing specialized tooling for other industries
-
Energy Sector
- Manufacturing parts for oil and gas exploration tools
-
Consumer Goods
- Producing molds for plastic products
-
Applications that require
- Complex 3D cavities and shapes
- Blind cavities and keyways
- Internal splines and treads
- Deep ribs and sharp inside corners
Conventional EDM Hole Drilling
Conventional EDM hole drilling is almost a combination of wire EDM and sinker EDM. Like wire EDM, hole drilling EDM is very precise and produces smooth surface finishes; however, a straight electrode is required to “cut” the hole in the workpiece.
This specialized EDM process has a number of advantages and disadvantages, including:
Pros |
Cons |
Specialized for creating precise, deep holes | Limited to creating round holes |
Can “drill” holes in hard, conductive materials that are difficult to machine conventionally | Slower process compared to conventional drilling for simple holes |
Capable of producing small-diameter holes with high aspect ratios | Higher equipment and operational costs compared to traditional drilling |
No mechanical stress on the workpiece | Requires a workpiece made from a conductive material |
Materials
Materials well-suited for hole drilling EDM include aluminum and its alloys, brass, conductive ceramics, copper and copper alloys, exotic metals, molybdenum, nickel alloys, titanium, and tungsten carbide.
Industry Applications
Many industries benefit from hole drilling EDM’s tight tolerances.
-
Aerospace
- Cooling holes in turbine blades and vanes
-
Automotive
- Precision holes in engine components
-
Medical Devices
- Holes for drug delivery systems
-
Electronics
- Creating openings for fiber optic components
-
Mold and Die Making
- Cooling channels in molds and dies
-
Cutting Tool Industry
- Drilling holes for inline cooling and flushing in cutting tools
-
Research and Development
- Fabricating holes for particle sensors and accelerator components
-
Optics
- Drilling holes in lens arrays and optical assemblies
Miro’s Wire EDM Machining Services
We are proud to offer wire EDM and small-hole EDM drilling as part of our machining services. Our state-of-the-art submersible wire EDM machines can achieve a tolerance of ± 0.0001 and offer a large travel range, allowing us to machine an array of components. Because wire EDM is such an efficient and effective method for cutting hard materials and complex designs, we often use it to machine tool steel and other compatible conductive materials that our other machining methods can’t handle.
The incredible precision our submersible wire EDM delivers makes it a top process for industries that require tight tolerances like non-implant durable medical equipment manufacturing and that have intricate components. Because our machines require little human intervention, they are able to operate continuously to meet demanding production schedules.
The Miro Difference
At Miro, your pains are our pains. When you partner with us, you don’t have to worry about working with multiple manufacturers to complete your project or ever wonder how your project is going. “From start to part,” we streamline the manufacture of your components and communicate often.
We strive to be a true partner for our customers to streamline their operations and help them grow. We do this by solving these common pains: having to send out a workpiece or part to multiple manufacturers for completion, manufacturing partners that don’t communicate authentically or at all, manufacturing that takes too long, and finding ways to re-shore their manufacturing.
How do we solve these pain points for our customers? It’s in our tagline “from start to part.” As a one-stop shop contract manufacturing partner, we simplify the whole process for our customers – from design to finished part – with extensive communication and collaboration along the way. Let us quote your wire EDM machining project and experience the Miro difference for yourself: https://www.miromfg.com/rfq/.